Trick Advantages and Factors To Consider of Executing Plastic Extrusion in Your Projects
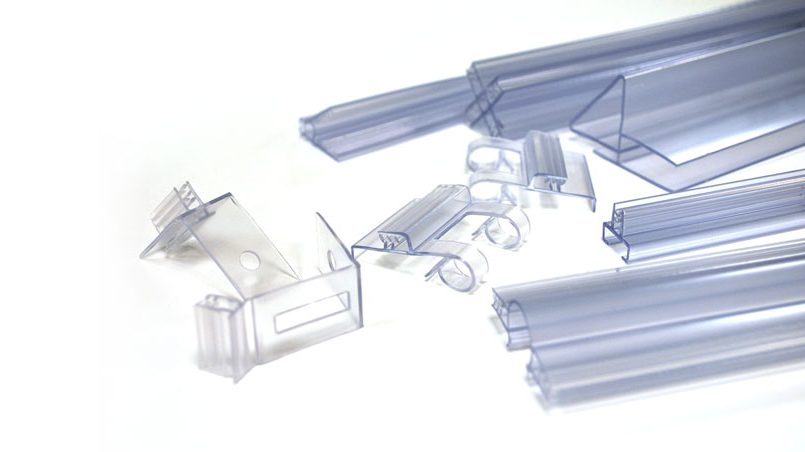
Understanding the Basics of Plastic Extrusion
Plastic extrusion, a staple in the production industry, is a procedure that includes melting raw plastic product and reshaping it right into a continual profile. The charm of plastic extrusion lies in its adaptability. The option of plastic and the layout of the die figure out the product's qualities.

The Economic Advantage of Plastic Extrusion
The economic benefit of plastic extrusion exists primarily in two locations: affordable material production and valuable production rates. With plastic extrusion, organizations can generate high volumes of product at a reduced expense contrasted to other techniques. Additionally, the procedure flaunts a remarkable production rate, significantly minimizing time and more improving its financial practicality.
Affordable Material Production
A substantial benefit of plastic extrusion is its impressive cost-effectiveness. This manufacturing process allows for constant, high-volume production with marginal waste, which equates right into lower costs. The raw materials utilized, generally plastic pellets, are fairly low-cost compared to other materials (plastic extrusion). The process itself requires less energy than several various other production techniques, additionally lowering prices. In addition, the extrusion process permits a high level of accuracy in shaping the plastic, reducing the need for pricey post-production modifications or modifications. Additionally, the toughness and long life of extruded plastic products frequently imply less require for substitutes, contributing to long-term savings. All these variables make plastic extrusion a very cost-effective choice for many tasks, using an appealing balance in between cost and efficiency.
Beneficial Production Speeds
While maintaining the cost-effectiveness of the materials, an additional significant advantage of plastic extrusion depends on its rapid production speeds. This efficiency in the manufacturing procedure is credited to the constant nature of the extrusion process, permitting for high-volume manufacturing in a reasonably short time span. The rate of manufacturing directly associates to a reduction in labor prices and a boost in result, thus boosting the overall economic feasibility of the process. The busy production does not endanger the quality of the final product, making certain consistent and trustworthy outcomes. This mix of cost-effectiveness, high quality, and rate highlights the considerable economic advantage of applying plastic extrusion in numerous projects.
Versatility and Customization: The Strengths of Plastic Extrusion
One of the prominent staminas of plastic extrusion lies in its convenience and personalization possibility. These top qualities open the door to limitless design opportunities, providing makers the ability to tailor items to certain needs. This heightened degree of customization not just improves product capability however also significantly boosts item individuality.
Endless Style Possibilities
Plastic extrusion beams in its capability to offer virtually unlimited design opportunities. This technique offers freedom to create intricate profiles and intricate shapes, a feat difficult to achieve with other fabrication techniques. Owing to the fluid nature of liquified plastic, the process is versatile enough to yield a diverse about his variety of sizes, kinds, and dimensions. The plastic can be manipulated to match distinct requirements, enabling the manufacturing of tailored geometries and meeting certain client demands. Plastic extrusion can deal with look here a variety of plastic kinds, increasing its application scope. This adaptable method, therefore, serves a variety of industries from building to auto, packaging to electronics, and beyond. With plastic extrusion, the style possibilities are basically countless.
Increasing Product Individuality
The adaptability of plastic extrusion can substantially boost product individuality. This process enables designers to explore different shapes, sizes, and colors, providing the flexibility to produce special items that stick out in the marketplace. It is this modification that offers a distinctive identification per item, distinguishing it from its competitors.
In addition to its visual advantages, the customizability of plastic extrusion additionally provides practical advantages. Therefore, plastic extrusion not only boosts item originality however also its utility and marketability.
Design Limitations in Plastic Extrusion: What You Required to Know
Just how can make limitations possibly impact the procedure of plastic extrusion? While plastic extrusion is versatile, style constraints can reduce its advantages. Specific complex styles might not be practical because of the constraints of the extrusion process, potentially restricting the production of elaborate accounts. The process is much less suitable for multi-chambered or hollow frameworks. Additionally, the extrusion process might not constantly give the desired surface area finish, specifically for those needing high gloss or optical quality. Material option can also posture difficulties, as not all polymers appropriate for extrusion. High-temperature resistant plastics, for example, may present troubles. Understanding these constraints is important for reliable implementation of plastic extrusion in your projects. plastic extrusion.
Examining the Ecological Influence of Plastic Extrusion
While understanding design limitations is a considerable facet of plastic extrusion, it is similarly essential to consider its ecological ramifications. The procedure of plastic extrusion includes melting plastic materials, possibly launching damaging gases into the setting. Utilizing recycled plastic products in the extrusion procedure can lower environmental impact.

Case Research: Effective Projects Using Plastic Extrusion
Success stories additional reading in the area of plastic extrusion are plentiful, showing both the adaptability and efficiency of this production process. plastic extrusion. Another effective situation is the manufacturing of plastic movie for product packaging and farming. These instances show plastic extrusion's important role in different industries, proving to its adaptability, cost-effectiveness, and trustworthy result.
Verdict
In conclusion, plastic extrusion offers a reliable and cost-effective technique for generating complicated shapes with marginal waste. While it supplies many advantages such as cost-effectiveness and versatility, it's vital to think about possible design constraints and environmental results. Implementing naturally degradable or recycled products can reduce these issues, enhancing sustainability. Integrating plastic extrusion into tasks can cause effective outcomes, as evidenced by many study.
Plastic extrusion, a staple in the manufacturing market, is a procedure that involves melting raw plastic material and improving it into a continual account. Plastic extrusion can handle a range of plastic kinds, expanding its application extent.Just how can design restrictions potentially influence the process of plastic extrusion? The process of plastic extrusion includes melting plastic materials, potentially launching unsafe gases right into the environment. Utilizing recycled plastic materials in the extrusion procedure can decrease environmental effect.